What is Pump Cavitation and How Do I Avoid It?
- Zack Woo
- Jul 15, 2024
- 9 min read
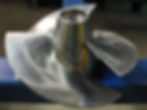
Pump cavitation is the formation and collapse of vapor bubbles in a pump, which can cause cavitation damage and create shock waves that harm the pump's components. You can avoid it by ensuring that the net positive suction head (NPSH) available is greater than the NPSH required by the pump.
What causes cavitation in a pump?: Vapor Pressure, Cavitation Bubbles & Bubble Collapse
In a pump, the difference in vapor pressure causes cavitation, leading to the formation of cavitation bubbles. These bubbles develop when the liquid's pressure falls below its vapor pressure, most commonly near the impeller.
When these bubbles travel to areas of higher pressure, such as the metal surface within the pump, they undergo bubble collapse, also known as inertial cavitation.
This process creates shock waves that can severely damage the pump. Cavitation damage is often observed on the impeller and other metal surfaces.
Maintaining the proper net positive suction head and correctly regulating the discharge valve can help mitigate the effects of hydrodynamic cavitation.

What is cavitation in pumps?
In pumps, cavitation is the formation and subsequent collapse of vapor-filled cavities or "bubbles" within the liquid being pumped.
This typically occurs when the liquid's pressure falls below its vapor pressure, often at the pump suction, leading to the creation of cavitation bubbles.
Once these bubbles move into areas of higher pressure within the pump, they implode or collapse violently against the metal surface, causing cavitation damage.
This phenomenon generates shock waves that can erode the pump's components and significantly reduce its efficiency and lifespan.
The types of cavitation in centrifugal pumps include suction cavitation and discharge cavitation. Suction cavitation happens when the pump suction pressure is too low, usually due to a restricted suction pipe or a clogged filter, resulting in the formation of air bubbles.
Discharge cavitation occurs when there is a high discharge pressure, causing liquid to flow back towards the lower pressure at the pump's inlet, where cavitation bubbles can form.
Effective prevention strategies involve ensuring the net positive suction head available (NPSHa) exceeds the net positive suction head required (NPSHr) and maintaining proper suction pipe design and maintenance.
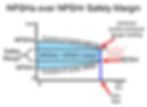
What are the types of pump cavitation?
The types of pump cavitation include vaporization cavitation, turbulence cavitation, Vane Syndrome cavitation, internal re-circulation, and air aspiration cavitation.
Vaporization cavitation, also referred to as classic cavitation, occurs when the static pressure in the pump falls below the liquid's vapor pressure, leading to the formation of cavitation bubbles.
Turbulence cavitation is often caused by irregular flow patterns which disrupt the smooth movement of liquid drops through the pump casing, resulting in bubble formation.
Vane Syndrome cavitation happens near the pump impeller vanes and is commonly linked to surface tension and hydrodynamic cavitation effects.
Internal re-circulation is characterized by the re-circulation of a liquid within the pump, contributing to the foaming liquid phenomenon and eventual cavitation.

Air aspiration cavitation is due to the ingress of air into the pump, subsequently creating air bubbles that collapse under varying atmospheric pressure conditions.
Additionally, suction cavitation arises when the pump suction pressure is too low, leading to cavitation bubble formation at the suction side.
Acoustic cavitation and ultrasonic cavitation are distinguished by their reliance on sound waves and high-frequency vibrations, respectively, often used in cleaning and medical equipment but detrimental in industrial pumps.
Nitrogen cavitation forms when excessive nitrogen is dissolved in the liquid, while discharge cavitation and inertial cavitation also play critical roles in the multi-faceted phenomenon.
Each form of cavitation poses unique challenges, necessitating tailored solutions to maintain efficient pump operations.

What are the 4 causes of cavitation in a pump?
In a pump, the 4 causes of cavitation include clogged filters and strainer, a flimsy hose, fluid viscosity, and excessively long inlet piping.
Cavitation in centrifugal pumps is frequently caused by issues such as a poorly specified pump, low pump suction pressure, and obstructions on the suction side.
When present, these factors allow bubbles to form and subsequently these bubbles collapse, causing cavitation damage to the metal surfaces of the pump housing.
The net positive suction head (NPSH) must be carefully managed to prevent these conditions. Pump cavitation also manifests through distinct sounds, often described as resembling gravel or marbles swirling inside the pump.
These noises occur due to bubbles collapsing near the pump impeller, transmitting vibrations through the pump housing and piping systems.
Inadequate discharge valve settings and increased discharge pressure can further exacerbate cavitation by altering head pressure dynamics.
Ensuring proper pump maintenance and specification of components is crucial to mitigating pump cavitation and maintaining efficient, reliable operation.

How to detect cavitation in pumps?
In pumps, cavitation can be detected by observing several symptoms, including unusual sounds, vibrations, temperature, power and performance changes.
As cavitation occurs, the energy forces bubbles to collapse, creating a distinct pump cavitation sound often described as a rattling or "marbles" noise.
This noise results from bubbles collapsing near the metal surface of the pump components. Vibration is another indicator, as cavitation increases, causing erratic movement due to fluctuating forces within the pump.
Monitoring the temperature and power detection of the pumped liquid can also reveal cavitation. Anomalies in temperature readings indicate higher energy losses and inefficiencies, while unexpected power consumption suggests increased resistance within the pump system.
Lower pressure on the suction side and reduced head pressure contribute to cavitation by drawing bubbles into the pump at critical points.
Additionally, significant drops in discharge pressure may signal ongoing cavitation. Changes in flow rate further exacerbate these conditions by disrupting the smooth movement of the liquid through the pump.
Effective detection and mitigation of cavitation are essential to maintaining efficient and reliable pump operations, necessitating a keen awareness of these symptoms and their underlying causes.

How to prevent pump cavitation in centrifugal pump?: Prevention of Pump Cavitation in Centrifugal Pumps
In a centrifugal pump, you can prevent cavitation by ensuring that the Net Positive Suction Head Available (NPSHa) exceeds the Net Positive Suction Head Required (NPSHr). This helps maintain sufficient hydrostatic pressure to avoid the formation of vapor bubbles.
Cavitation often occurs when heated liquids reach their boiling point under low pressure conditions, creating vapor bubbles that rapidly collapse and produce shock waves.
To avoid cavitation, it's essential to manage the pump system’s flow velocity, ensuring that it remains within optimal limits to prevent the formation of cavitation bubbles.
Additionally, maintaining an adequate discharge pressure can help avoid classic cavitation and vane syndrome.
For instance, in plunger pumps, proper maintenance of the intake and discharge systems is crucial to prevent bubble formation and collapse.

To avoid cavitation in turbines, maintaining a consistent centrifugal force and suitable NPSHr is vital.
Regular monitoring and adjustments of the pump’s suction line, such as minimizing air ingress to reduce air bubbles, can also significantly mitigate the risk of cavitation damage.
Ensuring that the pump's operational parameters stay within the recommended range, and avoiding sudden changes in demand that can cause drastic pressure shifts, are fundamental strategies.
By understanding the intricate balance between NPSHa and NPSHr, operators can effectively prevent discharge cavitation and protect their equipment from the harmful effects of cavitation bubbles collapsing.
Regular inspections and maintenance also help in early detection of cavitation symptoms, reducing potential damage and extending the pump’s lifespan.

How to avoid cavitation in pumps?
There are 5 types of pump cavitation. In pumps, you can avoid cavitation by:
Vaporization Cavitation
In pumps, you prevent vaporization cavitation by ensuring the liquid temperature does not approach its vapor pressure.
Pump manufacturers recommend installing a booster pump to maintain a high pump suction head and increasing the eye diameter of your pump impeller to minimize the formation of cavitation bubbles.
Regularly check the pumped liquid level and flow rate to avoid insufficient liquid supply.
Turbulence Cavitation
In pumps, you prevent turbulence cavitation by reducing poorly developed flow and unnecessary turbulence.
This can be achieved by designing smooth suction piping and ensuring the suction inlet is properly aligned.
Pump manufacturers suggest using pump components with streamlined geometries and maintaining optimal flow velocity.
Vane Syndrome Cavitation
In pumps, you prevent vane syndrome cavitation by avoiding vane syndrome caused by sharp changes in flow direction.
Ensure that the pump impeller is properly designed and free from blockages.
Address any issues with pump components that could cause flow disruptions and work with the pump manufacturer to fine-tune the system. Inspections for clogged filters and other pump components should be routine.
Internal Re-circulation
In pumps, you prevent cavitation by addressing internal re-circulation at the impeller’s suction and discharge sides.
Adjust the pump casing and suction head to blunt the effects of internal re-circulation. Install a check valve to prevent backflow and ensure that the pump system maintains a steady flow rate.
Ensuring the pump impeller and other components are correctly sized and installed helps mitigate this issue.
Air Aspiration Cavitation
In pumps, you prevent cavitation by eliminating sources of air bubbles in the pumped liquid. Tighten joint rings, secure secondary mechanical seals, and monitor the suction piping for any air leaks.
Make sure that the suction pipe is free from blockages and check the suction inlet and suction head for potential air ingestion points.

What is the most common cause of pump cavitation?
The most common cause of pump cavitation is the presence of clogged filters and strainers, which restrict the fluid flow and increase fluid velocity, leading to a drop in fluid pressure at the pump inlet.
This can result in the formation of cavitation bubbles, causing the cavitation phenomenon. Factors such as fluid viscosity, a flimsy hose, and a flooded inlet, contribute to the issue as well.
High velocity and flow separation further exacerbate the problem by creating areas of low pressure that induce pump cavitate/ cavitation.
The subsequent high power consumption and the generation of shock waves can damage pump components. Higher pressure in the high pressure discharge side can also cause fluid pressure imbalances, leading to cavitation.
To prevent these issues, it is essential to maintain unobstructed suction conditions and routinely inspect and maintain the pump system. Discover what are the benefits of routine maintenance for pumps and when is it time to upgrade a water pump.
Pump cavitation often occurs in the oil and gas industry, where maintaining optimal fluid flow is critical for efficient operation. Find out where are water pumps commonly used in industrial settings.
Yes, other types of pumps can also experience cavitation, including centrifugal and positive displacement pumps, if the operational conditions lead to low pressure and the formation of vapor bubbles within the pump. Identify what are the different types of pumps in Singapore and what are the key components of a water pump.

How do you prevent cavitation in a hydraulic pump?
In a hydraulic pump, you prevent cavitation by working closely with the pump manufacturer to ensure all components are optimized for performance and the system is free from blockages such as clogged filters.
To combat cavitation, it is essential to maintain a well-developed inlet flow characterized by laminar flow and adequate suction pressure.
To maintain laminar flow, connect 5-10 pipe diameters of straight piping to the pump inlet. Do not include elbows, reducers, valves, or strainers within the final length of pipework.
Connecting an elbow directly to the pump flange, for example, draws fluid towards the outer curve of the elbow instead of directly into the eye of the impeller.
Lower pressure areas can be minimized by ensuring that the primary pump operates with care to promote higher pressure on the discharge side.
Regularly check the suction side, including the suction pipe and suction inlet, for any obstructions or damage, and make sure the shut-off valve is functioning correctly.
Utilizing proper piping materials, such as 100R4 or SAER4, and monitoring for air ingress around joint rings and secondary mechanical seals can also help.
Be aware that when poorly developed flow enters the pump’s suction inlet, it can lead to high velocity fluid regions, which might lower viscosity and exacerbate the problem.
Maintaining an optimal balance between system parameters will help prevent cavitation and extend the life of the hydraulic pump.

Does priming a pump prevent cavitation?
No, priming a pump does not prevent cavitation. Cavitation occurs when the suction reaches atmospheric pressure, and vacuum bubbles form.
When the local pressure falls below the vapor pressure of the fluid, a cavitation nucleus can form, initiating cavitation even if the pump has been properly primed.
As cavitation increases, the pressure differential within the pump creates shock waves as these bubbles collapse.
This cavitation occurs frequently around the pump impeller, where the rapid movement reduces local pressure and allows air bubbles to form and burst violently.
These shock waves can damage the impeller, leading to reduced efficiency and possible failure.
To effectively prevent pump cavitation, it's essential to follow guidelines set by the pump manufacturer, which may include adjusting the flow rate to ensure the local pressure remains above the vapor pressure threshold and considering the design of the entire system to mitigate low-pressure zones that may initiate cavitation bubbles.
Other issues that can affect pump performance include wear and tear on the mechanical seals, misalignment of pump components, and inadequate lubrication, which can all lead to reduced efficiency and potential equipment failure. Identify what are the common water pump problems and solutions and what are the symptoms and signs of a bad water pump.